Search
materials and coatings
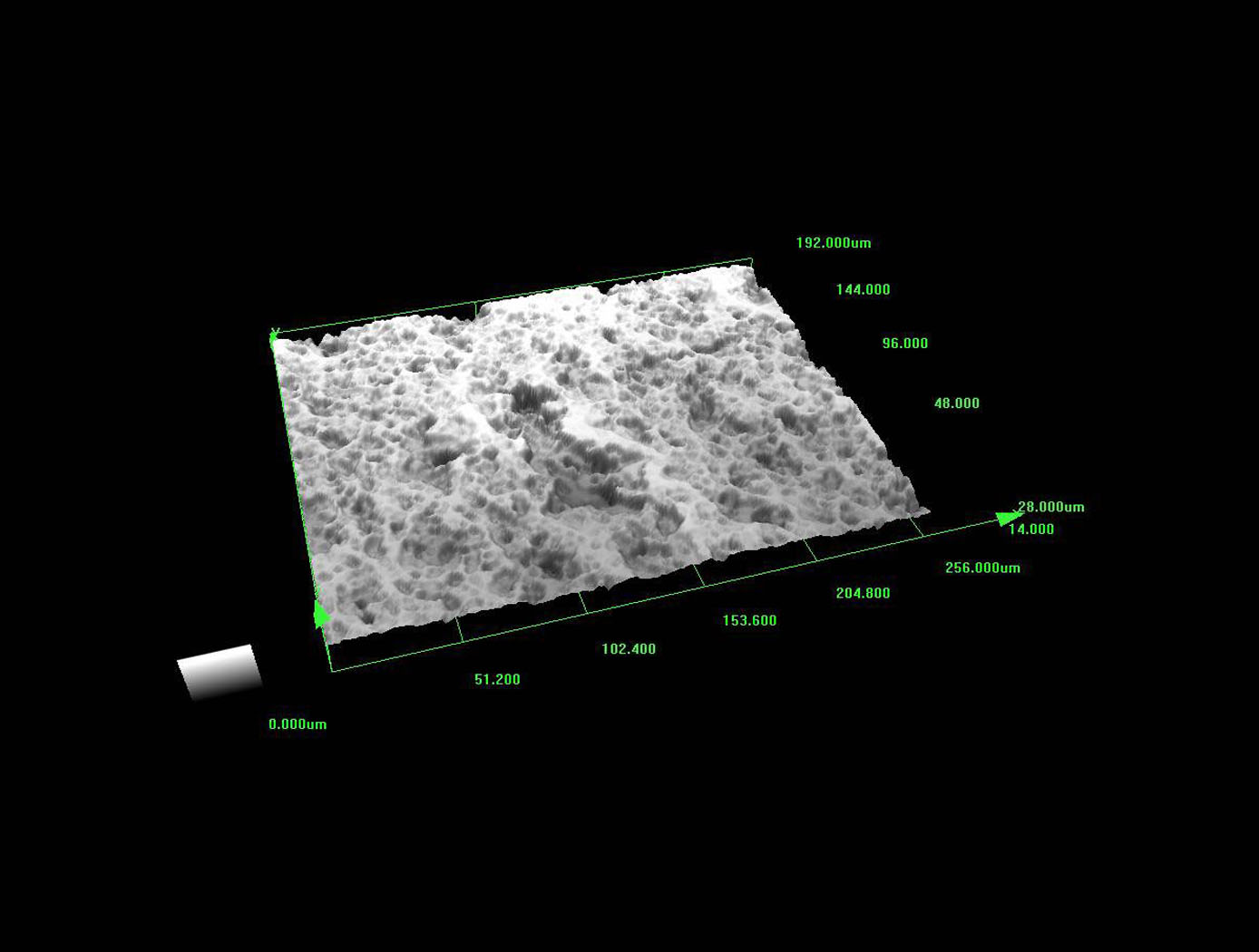
Molecular Adsorber Coating (MAC)
MAC is a zeolite based coating that captures and traps molecules in its microscopically porous structure. This microscopic nano-textured structure, consisting of large open pores or cavities, within a crystal- like structure, provides a large surface area to mass ratio that maximizes available trapping efficiency. MAC is a durable coating that is applied through spray application.
These sprayable coatings eliminate the major drawbacks of puck type adsorbers (weight, size, and mounting hardware requirements), resulting in cost savings, mass savings, easier utilization, greater adsorber surface area, more flexibility, and higher efficiency.
This coating works in air, as well as vacuum systems, depending on the application. There is potential for ground based spin-off applications of this coating, particularly in areas where contaminants and volatile compounds need to be collected and contained. Example industries include: pharmaceutical production, the food industry, electronics manufacturing (circuit boards and wafers), laser manufacturing, vacuum systems, chemical processing, paint booths, and general gas and water adsorption.
manufacturing
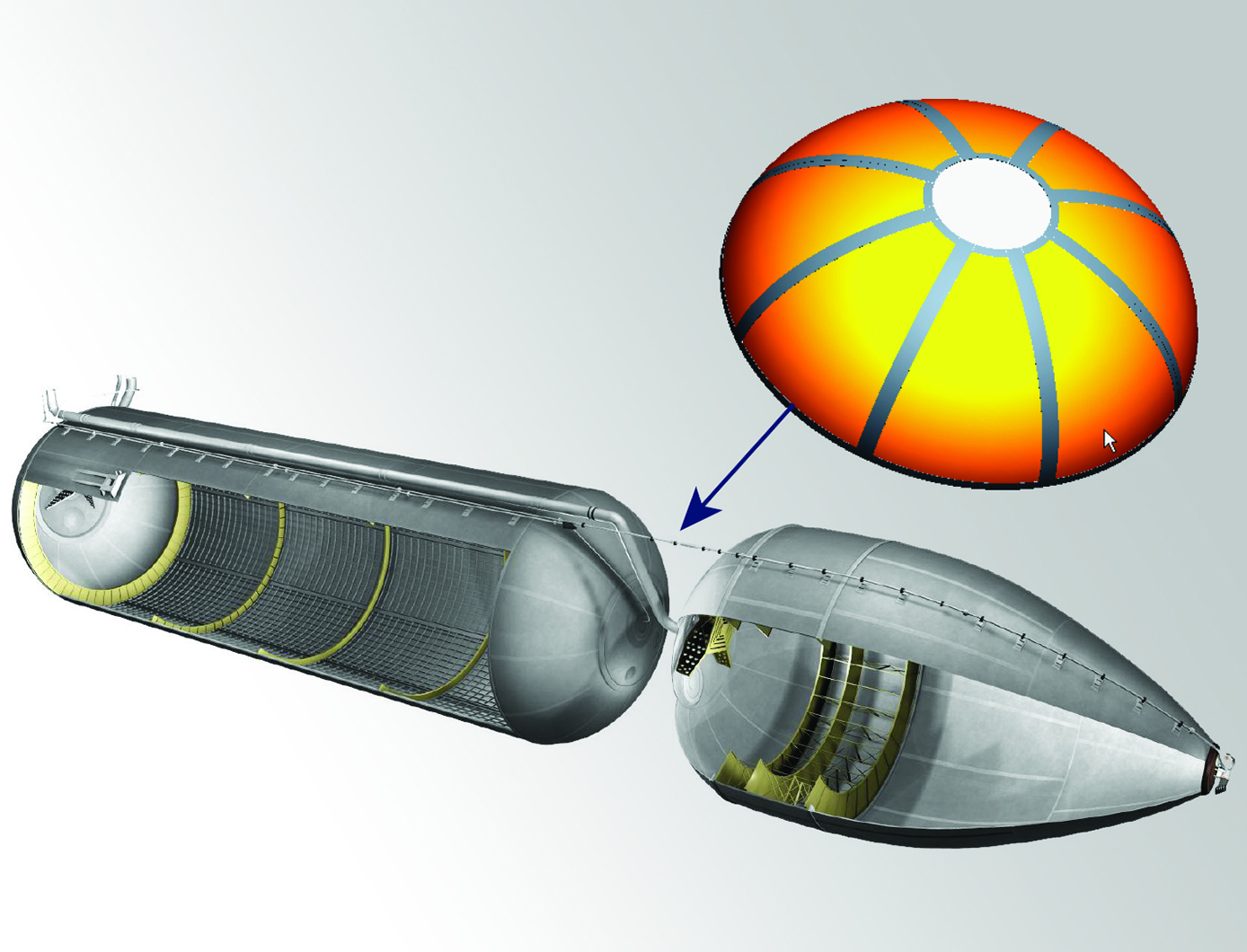
Improving Formability of Al-Li Alloys
Via this NASA innovation, a product is first heated to a temperature within the range of 204 to 343 degrees C for an extended soak of up to 16 hours. The product is then slowly heated to a second temperature within the range of 371 to 482 degrees C for a second soak of up to 12 hours. Finally, the product is slowly cooled to a final soak temperature of 204 to 343 degrees C before cooling to room temperature. The product so treated will exhibit greatly improved formability.
To date, the low formability issue has limited the use of lightweight Al-Li alloys for large rocket fuel tank dome applications. Manufacturing a dome by stretch forming typically requires multiple panels as well as multiple welding and inspection steps to assemble these panels into a full-scale fuel tank dome. Complex tensile and bending stresses induced during the stretch forming operations of Al-Li alloys have resulted in high rates of failure for this process. To spin form a large rocket dome, the spin blank must be prepared by joining smaller plates together using friction stir welding. However, friction stir welding produces a distinct metallurgical structure inside and around the friction stir weld that makes it very susceptible to cracking during spin forming.
materials and coatings
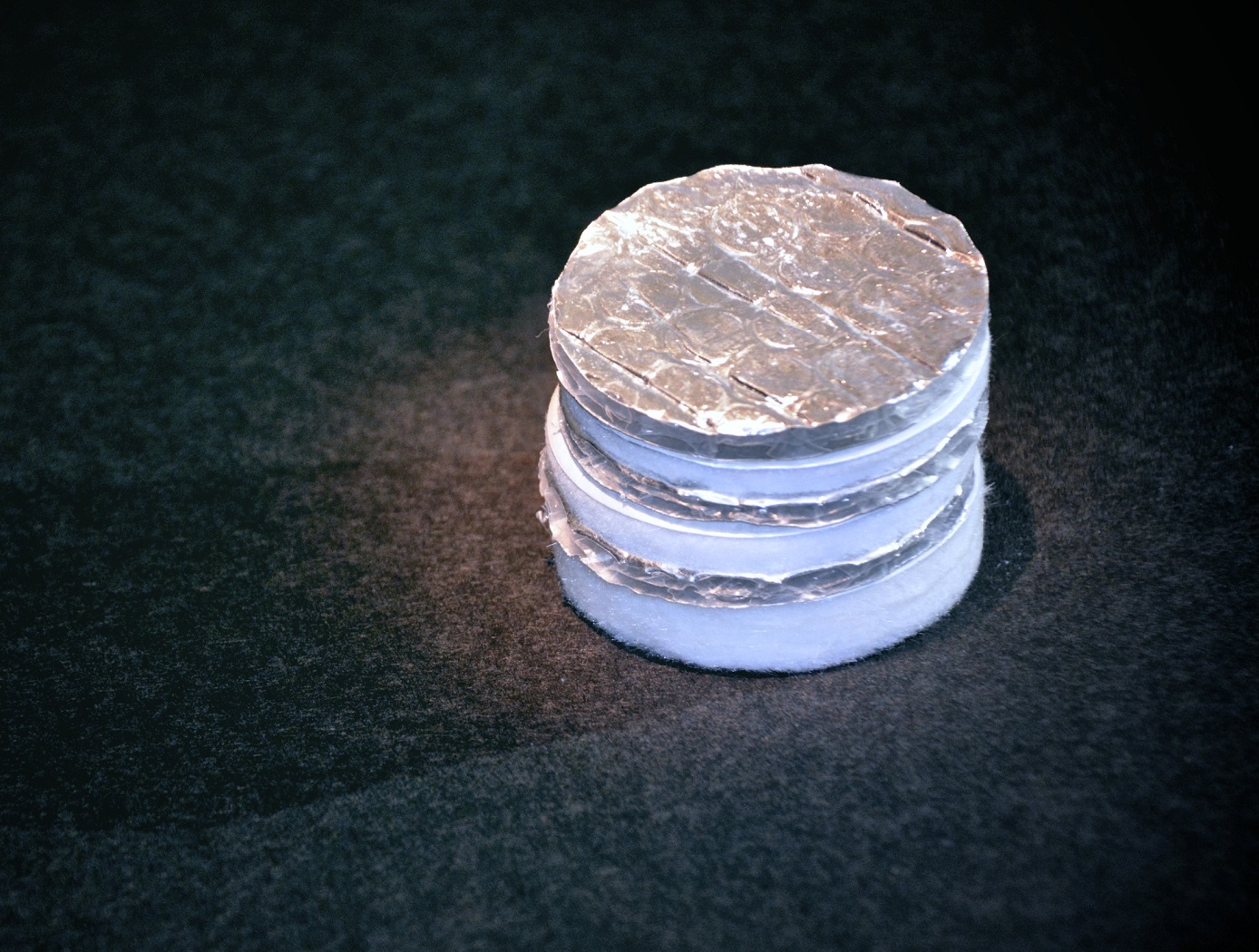
Layered Composite Insulation for Extreme Conditions (LCX)
The approach in developing the LCX system was to provide a combination of advantages in thermal performance, structural capability, and operations. The system is particularly suited for the complex piping, tanks, and apparatus subjected to the ambient environment common in the aerospace industry. The low-cost approach also lends the same technology to industrial applications such as building construction and chilled-water piping. The system can increase reliability and reduce life cycle costs by mitigating moisture intrusion and preventing the resulting corrosion that plagues subambient-temperature insulation systems operating in the ambient (humidity and rain) environment. Accumulated internal water is allowed to drain and release naturally over the systems normal thermal cycles. The thermal insulation system has a long life expectancy because all layer materials are hydrophobic or otherwise waterproof. LCX systems do not need to be perfectly sealed to handle rain, moisture accumulation, or condensation.
Mechanically, the LCX system not only withstands impact, vibration, and the stresses of thermal expansion and contraction, but can help support pipes and other structures, all while maintaining its thermal insulation effectiveness. Conventional insulation systems are notoriously difficult to manage around pipe supports because of the cracking and damage that can occur. Used alone or inside another structure or panel, the LCX layering approach can be tailored to provide additional acoustic or vibration damping as a dual function with the thermal insulating benefits. Because LCX systems do not require complete sealing from the weather, it costs less to install. The materials are generally removable, reusable, and recyclable, a feature not possible with other insulation systems. This feature allows removable insulation covers for valves, flanges, and other components (invaluable benefits for servicing or inspection) to be part of original designs.
Thermal performance of the LCX system has been shown to equal or exceed that of the best polyurethane foam systems, which can degrade significantly during the first two years of operation. With its inherent springiness, the system allows for simpler installation and, more importantly, better thermal insulation because of its consistency and full contact with the cold surface. Improved contact with the cold surface and better closure of gaps and seams are the keys to superior thermal performance in real systems. Eliminating the requirement for glues, sealants, mastics, expansion joints, and vapor barriers provides dramatic savings in material and labor costs of the installed system.
communications
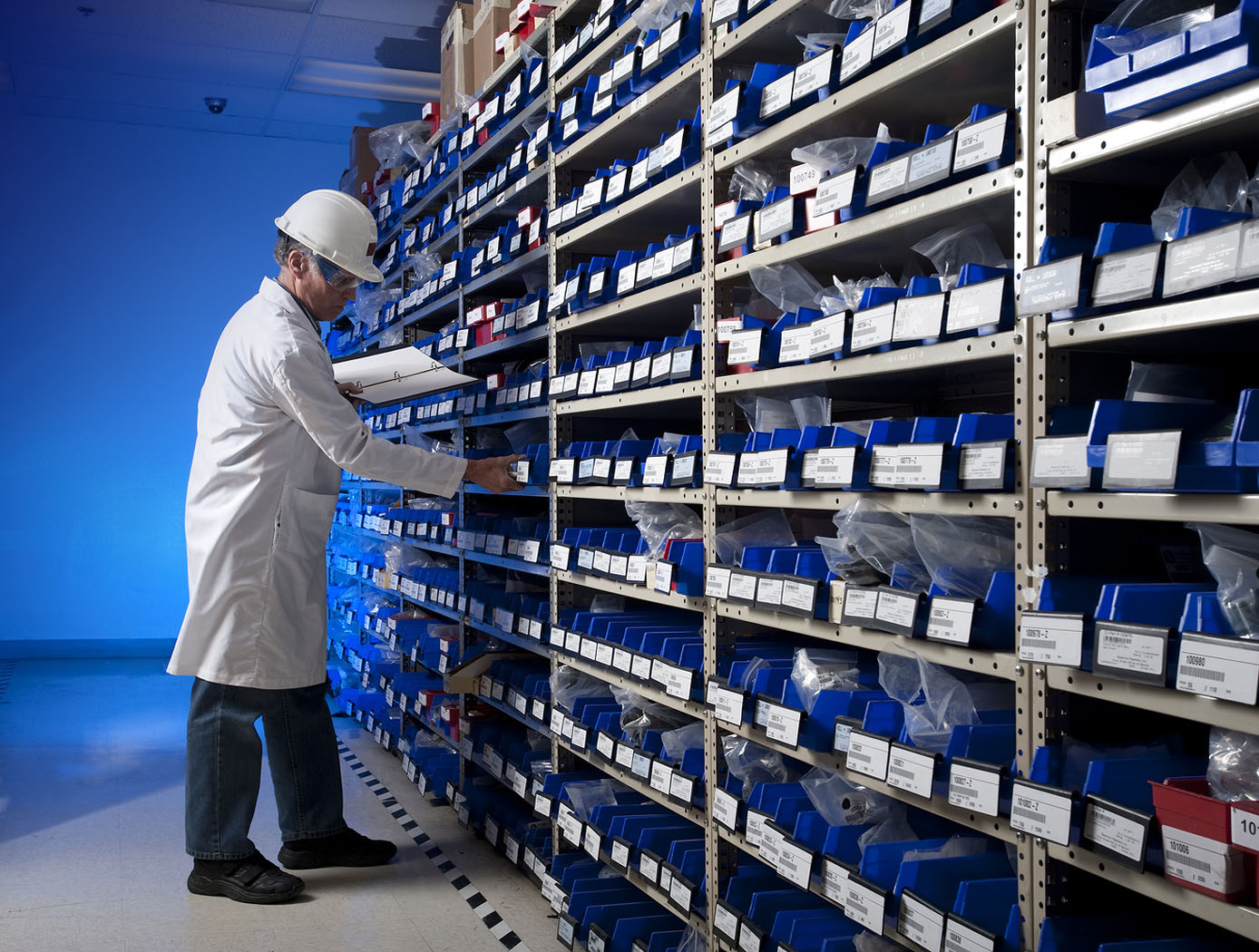
Smart Enclosure using RFID for Inventory Tracking
The smart enclosure innovation employs traditional RFID cavities, resonators, and filters to provide standing electromagnetic waves within the enclosed volume in order to provide a pervasive field distribution of energy. A high level of read accuracy is achieved by using the contained electromagnetic field levels within the smart enclosure. With this method, more item level tags are successfully identified compared to approaches in which the items are radiated by an incident plane wave. The use of contained electromagnetic fields reduces the cost of the tag antenna; making it cost-effective to tag smaller items.
RFID-enabled conductive enclosures have been previously developed, but did not employ specific cavity-design techniques to optimize performance within the enclosure. Also, specific cavity feed approaches provide much better distribution of fields for higher read accuracy. This technology does not restrict the enclosure surface to rectangular or cylindrical shapes; other enclosure forms can also be used. For example, the technology has been demonstrated in textiles such as duffle bags and backpacks. Potential commercial applications include inventory tracking for containers such as waste receptacles, storage containers, and conveyor belts used in grocery checkout stations.
materials and coatings

Multi-layered Self-healing Material System for Impact Mitigation
This innovation utilizes a tri-layered structure, comprised of solid plastic front and back layers sandwiching a viscous, reactive liquid middle layer. Combined, this system provides rapid self-healing following high velocity ballistic penetrations. Self-healing in the front and back layers occurs when the puncture event creates a melt state in the polymer materials and the materials melt elasticity snaps back and closes the hole. The viscous middle layer augments the self-healing properties of the other layers by flowing into the gap created by a ballistic puncture and concurrently solidifying due to the presence of oxygen. Thus, this innovation has two tiers of self-healing: a puncture-healing mechanism triggered by the projectile and a second mechanism triggered by the presence of oxygen.
Materials and Coatings
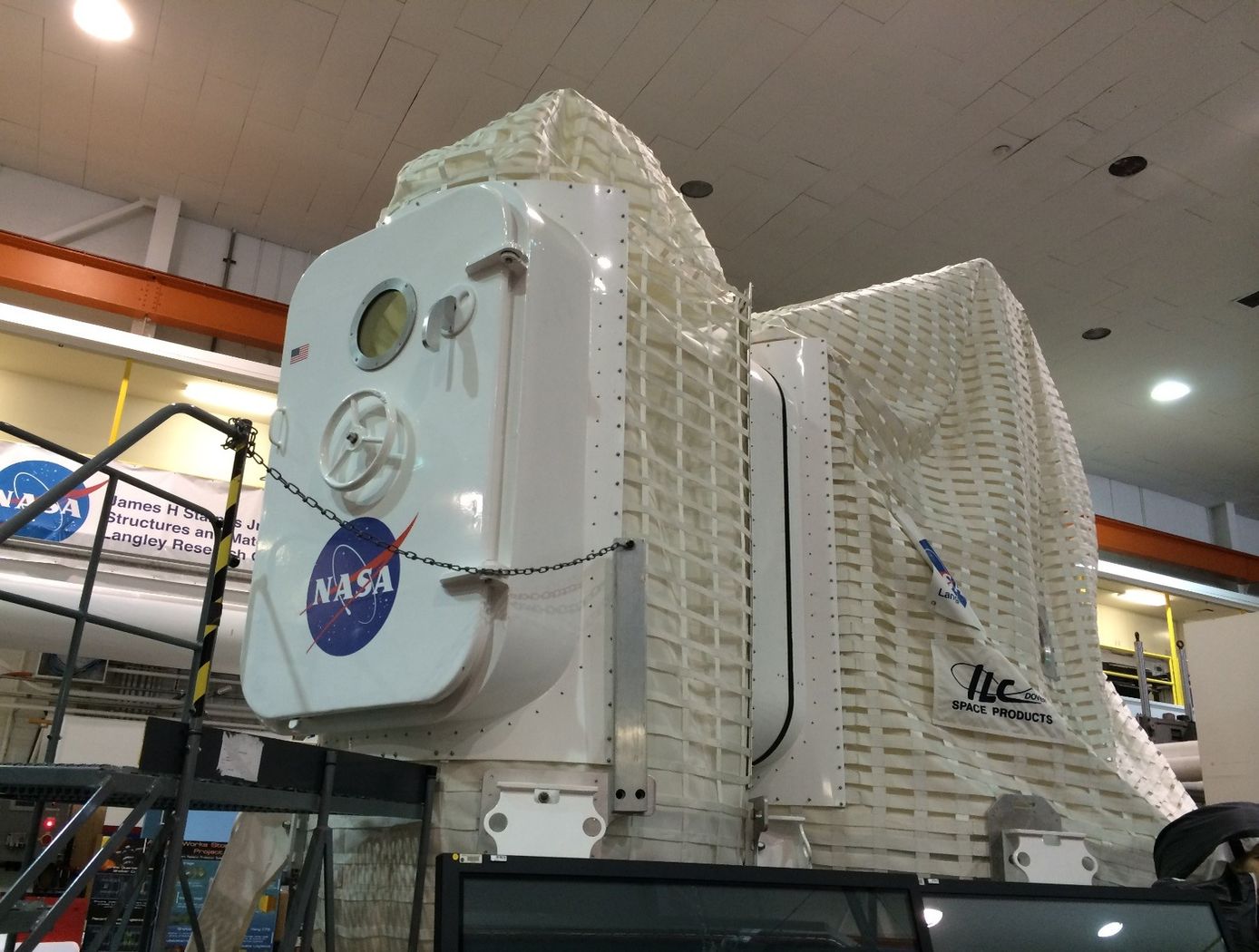
Mechanoresponsive Healing Polymers
The method chemically introduces mechanically sensitive chemical groups into the structure of a resin. By introducing mechanoresponsive functional groups to a polymer, it is possible to induce self-healing through the transformation of such chemical groups to where mechanical properties of a structure are almost completely restored. The forces imparted by a damage event can therefore be used to enable healing or repair of the structure.
Mechanical and Fluid Systems
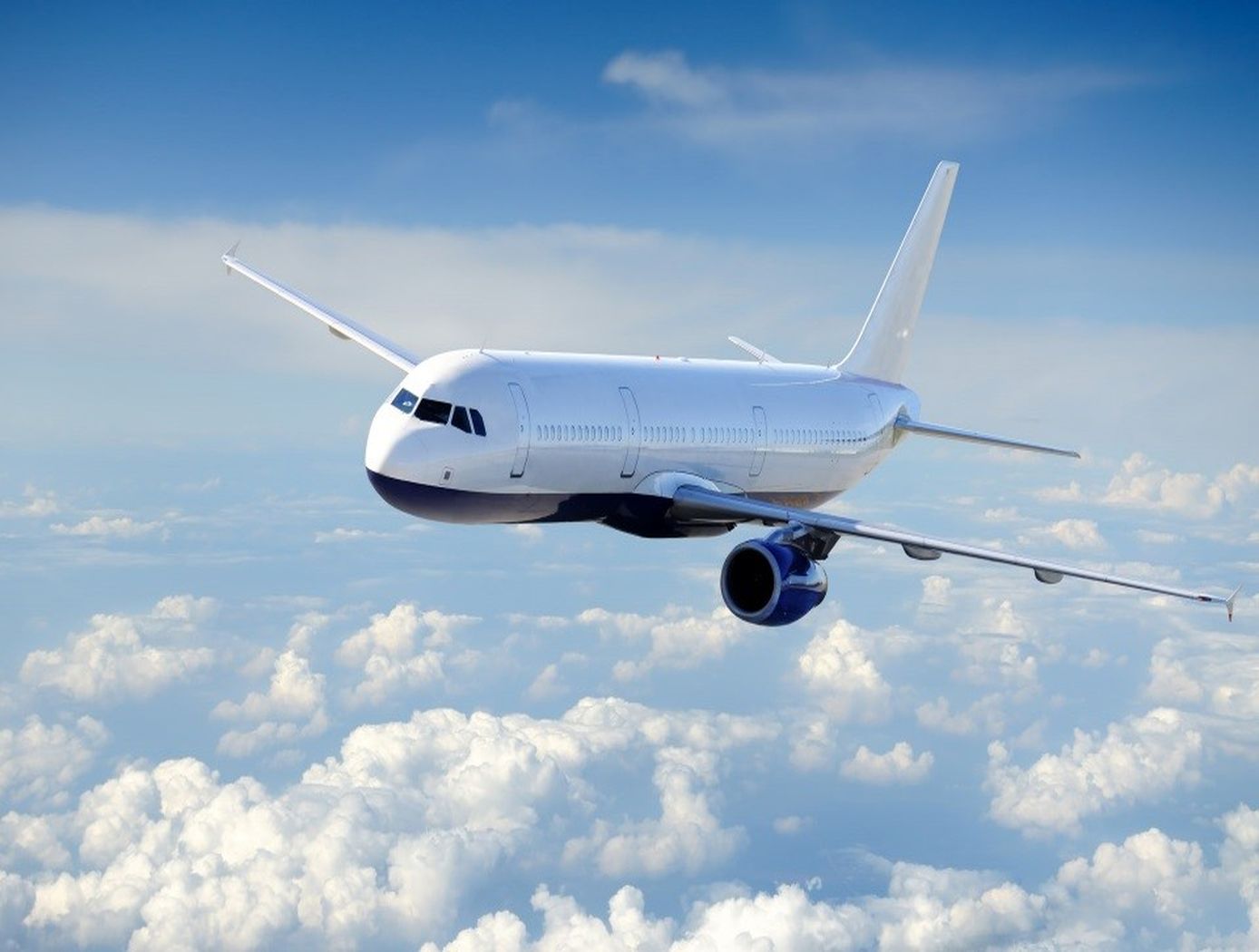
Healable Carbon Fiber Reinforced Composites
A composite fabrication process cycle was developed from composite precursor materials developed at LaRC to fabricate composite laminates. The precursor material is a pre-impregnated unidirectional carbon fiber preform, or prepreg. In the pre-pregging process, the high strength, structural reinforcing carbon fiber is wetted by a solution containing a self-healing polymer. The resulting material is of aerospace quality and exhibits a significant decrease of internal damage following impacts tests (using ASTM D 7137 standard).
Mechanical and Fluid Systems
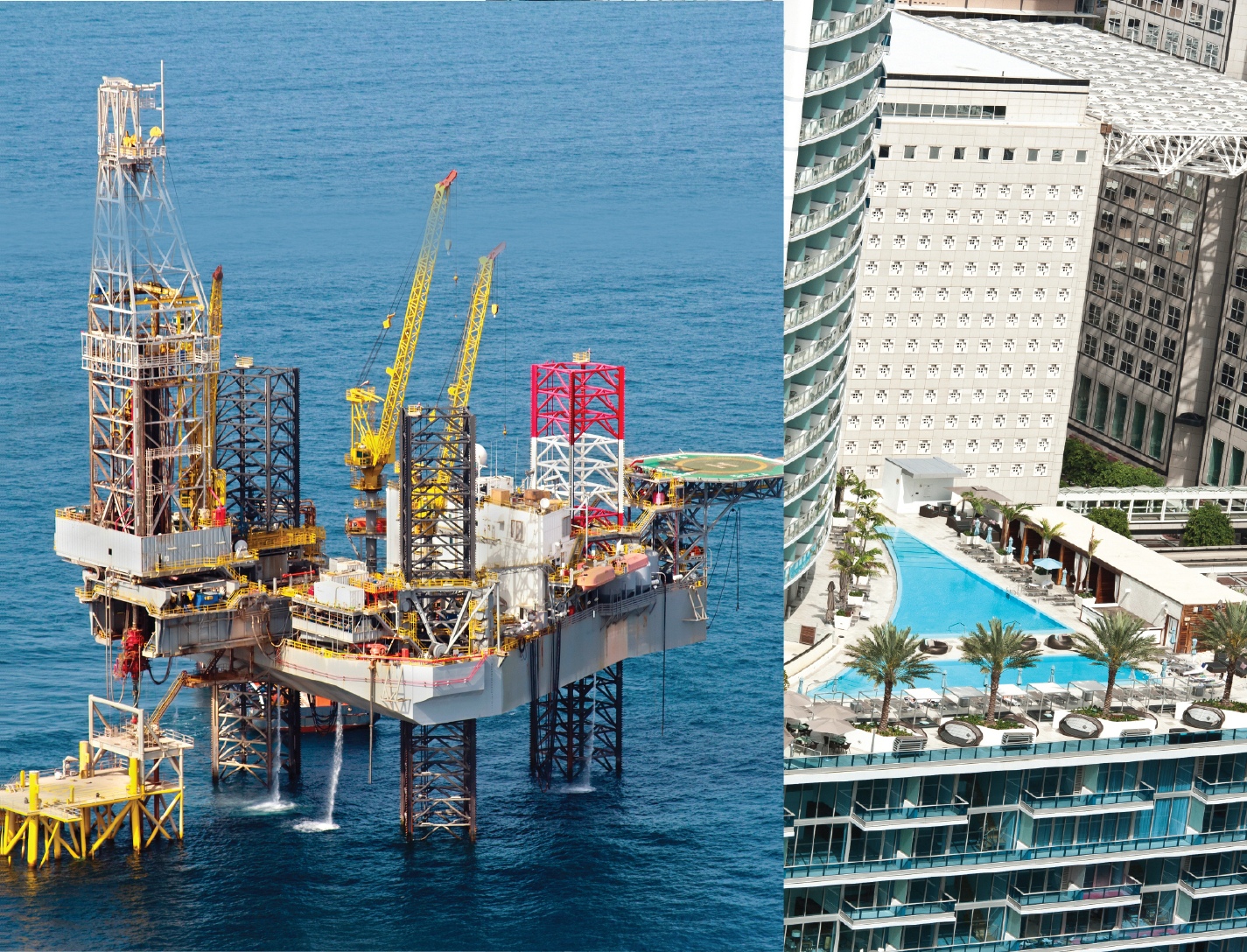
Fluid Structure Coupling Technology
FSC is a passive technology that can operate in different modes to control vibration:
Harmonic absorber mode: The fluid can be leveraged to act like a classic harmonic absorber to control low-frequency vibrations. This mode leverages already existing system mass to decouple a structural resonance from a discrete frequency forcing function or to provide a highly damped dead zone for responses across a frequency range.
Shell mode: The FSC device can couple itself into the shell mode and act as an additional spring in a series, making the entire system appear dynamically softer and reducing the frequency of the shell mode. This ability to control the mode without having to make changes to the primary structure enables the primary structure to retain its load-carrying capability.
Tuned mass damper mode: A small modification to a geometric feature allows the device to act like an optimized, classic tuned mass damper.
sensors
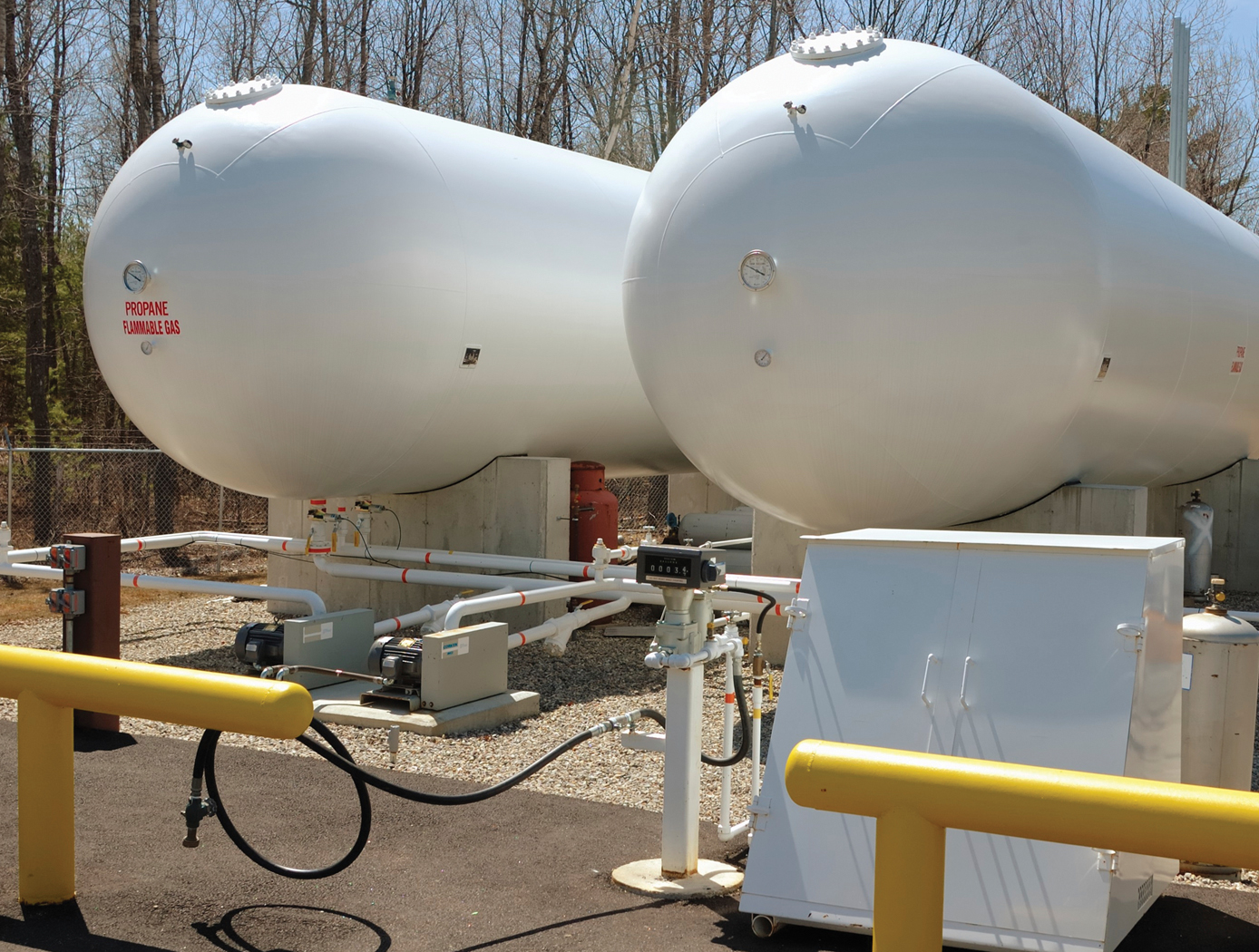
Low-Profile Wireless Sensor
The low-profile sensor is configured with a spiral electrical trace on flexible substrate. In typical inductor designs, the space between traces is designed to minimize parasitic conductance to reduce the impact of the capacitance to neighboring electronics. In the low-profile sensor, however, greater capacitance is desired to allow the operation of an inductor-capacitor circuit. This allows the traces to be closer together, decreasing the
overall size of the spiral trace.
The sensor receives a signal from the accompanying magnetic field data acquisition system. Once electrically active, the sensor produces its own harmonic magnetic field as the inductor stores and releases magnetic energy. The antenna of the measurement acquisition system is switched from a transmitting to a receiving mode to acquire the magnetic-field response of the sensor. The magnetic-field response attributes of frequency, amplitude, and bandwidth of the inductor correspond to the physical property states measured by the sensor. The received response is correlated to calibration data to determine the physical property measurement. When multiple sensors are inductively coupled, the data acquisition system needs to activate and read
only one sensor to obtain measurement data from all of them.
Sensors

Optical Mass Sensor for Multi-Phase Flows
Unlike commercial turbine and Venturi-type sensors, which are flow intrusive and prone to high error rates, NASA's new flow sensor technology uses an optical technique to precisely measure the physical characteristics of a liquid flowing within a pipe. It generates a reading of the flows density, which provides a highly accurate mass flow measurement when combined with flow velocity data from a second optical sensor.
NASA's sensor technology provides both a void fraction measurement, which is a measurement of the instantaneous gas/liquid percentage of a static volume and a quality measurement, which is the fraction of flow that is vapor as part of a total mass flow. It also provides a direct measurement of the gas/liquid concentration within the flow, making it suited for real-time measurement of multi-phase flows.
The technology was originally developed to accurately determine the flow rates and tank levels of multi-phase cryogenic fuels used on various NASA vehicles including the Space Shuttle and in ground-based propulsion testing. It can also be used for a wide range of gas/liquid ratios, flows with complex cross sectional profiles, flows containing bubbles or quasi-solids, and essentially any liquid, gas, or multi-phase flow that can be optically characterized. Because it is insensitive to position, the new technology also has potential for use in zero-gravity tank level sensors.